
As the rotational speed is proportional to the peripheral speed, a higher inclination reduces the needed rotational speed of the tool and workpiece, with a maximum possible angle at 45 degrees. More inclination means more cutting speed at the same peripheral speed v 1. Imagine a pinion meshing with a ring gear with collinear axes there will be no speed between the front face of the pinion and the ring. If the axis of the tool and the gear being made are parallel, there is no cutting speed being generated. The cutting speed vc (the relative speed between the front face of the cutting tool and the gear being made) is proportional to the inclination “E” between the tool axis and the gear axis (see Figure 1 and Figure 2), and the peripheral speed v 1 in the point of contact of the tool (“pinion”) and the gear. Mathematically more stringent explanations can be found in literature, for example, Reference. Here, basic mathematics is provided to explain power skiving principles in an intuitive way. The fixture has openings around the spindle for chip evacuation. The cutting action occurs on the front side of, in this case, the inserted cutting tool. Figure 1 shows the tool (on the left) inclined with respect to the ring gear both are spinning at high speed while meshing perfectly.
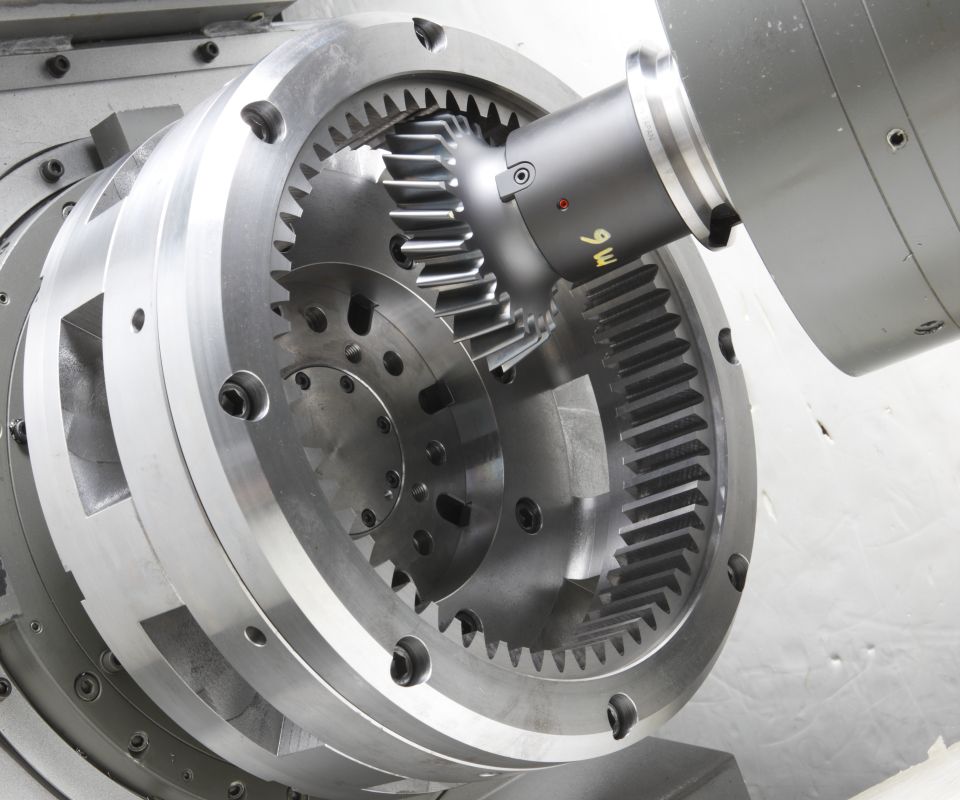
The cutting speed is generated by an inclination “E” between the axis of the gear being made and the axis of the tool. The front side of the tool (“pinion”) is sharp, and it cuts the gear while meshing. The difference is, while the tool that we can consider “the pinion” meshes with the gear, it is also pushed axially in the direction of the axis of the gear. This is the reason that an extremely accurate synchronization is needed between the workpiece spindle and the tool spindle. Power skiving is a continuous machining process where the tool meshes with the gear being made - similar to the way a pinion and gear mesh in a gear train. Power skiving is being seen as a viable alternative to broaching to manufacture internal gears (and external gears) since it is faster and more flexible than the other methods. A common way of making internal gears is shaping, which is a reciprocating method that’s much slower than both broaching and power skiving. Broaching is a fast and efficient method for internal gears and is well-suited for gears smaller than 8 inches, but is inflexible and uses large tools. Hobbing is only possible for external gears, while gashing is only possible for larger size internal ring gears from 6 inches (150 millimeters) and up to several feet in diameter using a special head in the hobbing machine. IntroductionĪ variety of methods exists for efficient gear manufacturing such as hobbing, gashing, and broaching.

To demystify power skiving, the following provides approximate yet valid ways to calculate required spindle speeds, which is key in machine and tool selection, as well as guidelines on what components are suitable for power skiving. To make power skiving a widely used method in gear and spline production, basic understanding of the method is needed.
Power skiving dmg products software#
Software now exists to define the form of the tool and the resulting component geometry, yet no basic rules of thumb or formulas are available in handbooks for the gear manufacturing engineer wanting to make a fast analysis on the viability of power skiving a particular component. The recent development in machine controls, machine hardware, and tool design have made it possible to apply the idea from 1910 on an industrial scale for making gears and splines. This article explains the fundamentals of power skiving in order to guide manufacturing engineers and decision-makers to determine when power skiving can be a suitable solution by using some simple mathematics and rules of thumb. Still, an understanding of even the basic principles may not be common knowledge within either the gear manufacturing or the general machining community. The same Japanese authors also published a JSME (Japan Society of Mechanical Engineers) paper where they describe gear skiving as a “high productivity method to produce internal gears with rotating tool.” There were few published works until about 2010 when literature appeared in forums such as The International Academy for Production Engineering (CIRP), International Journal of Advanced Manufacturing, American Society of Mechanical Engineers (ASME), and others, where power skiving was dissected and explained in sometimes quite heavy mathematical terms. Following a somewhat dormant period, a U.S. The initial solution was developed and patented in 1910 in Germany. The interest and successful application in power skiving is increasing within the gear manufacturing community as well as within companies that have access to modern five-axis machines but, thus far, have outsourced their gear manufacturing.
